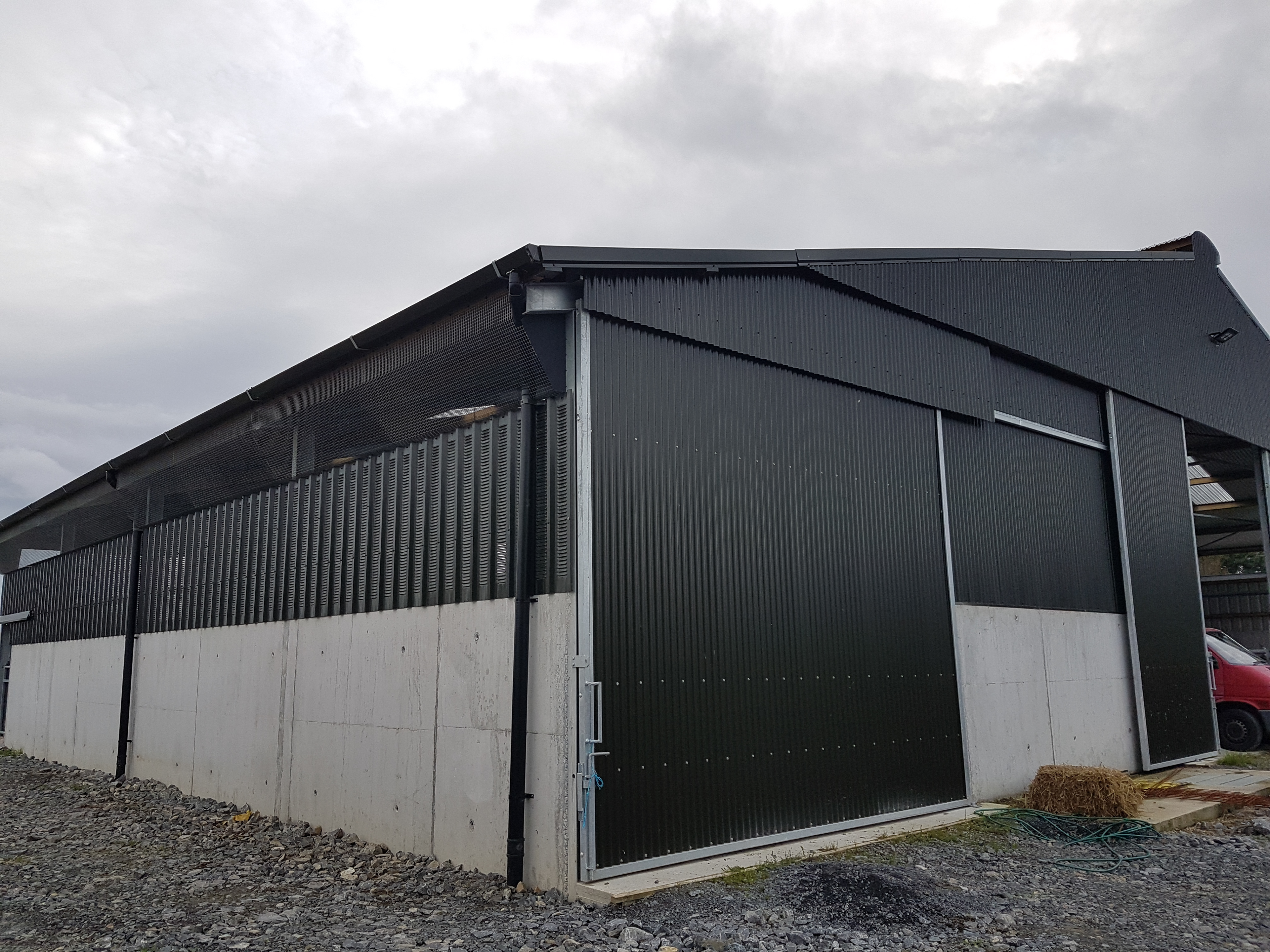
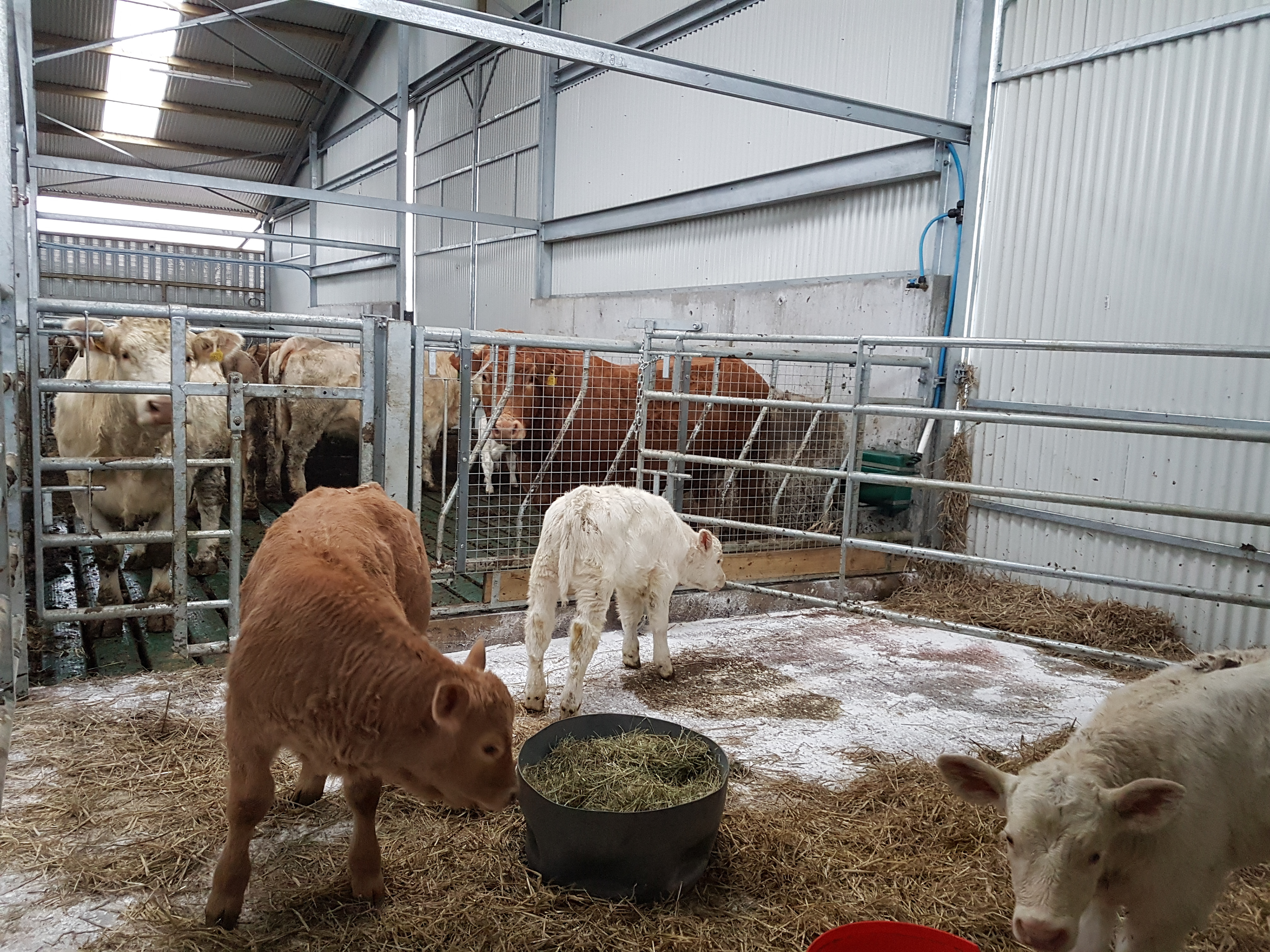
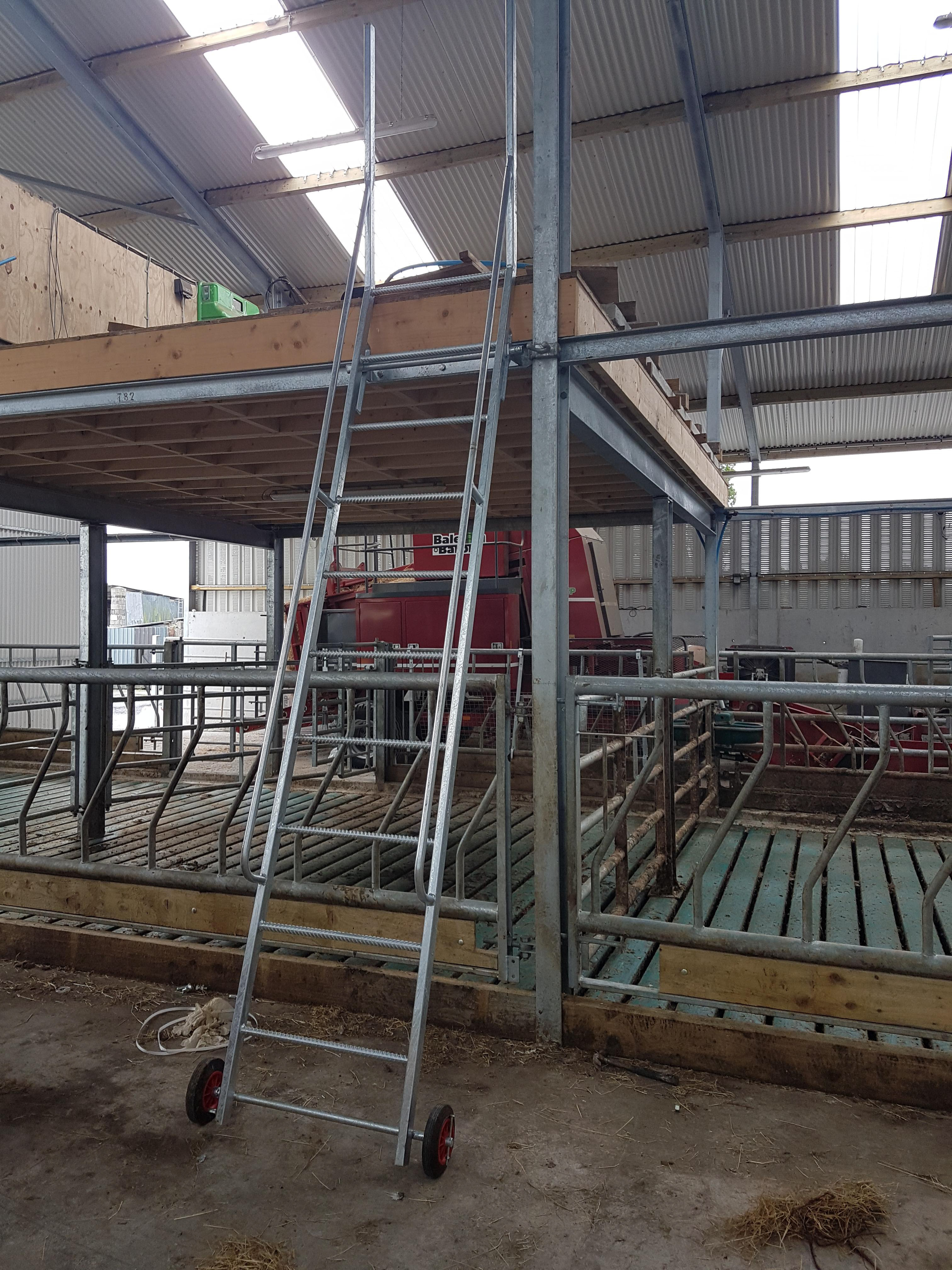
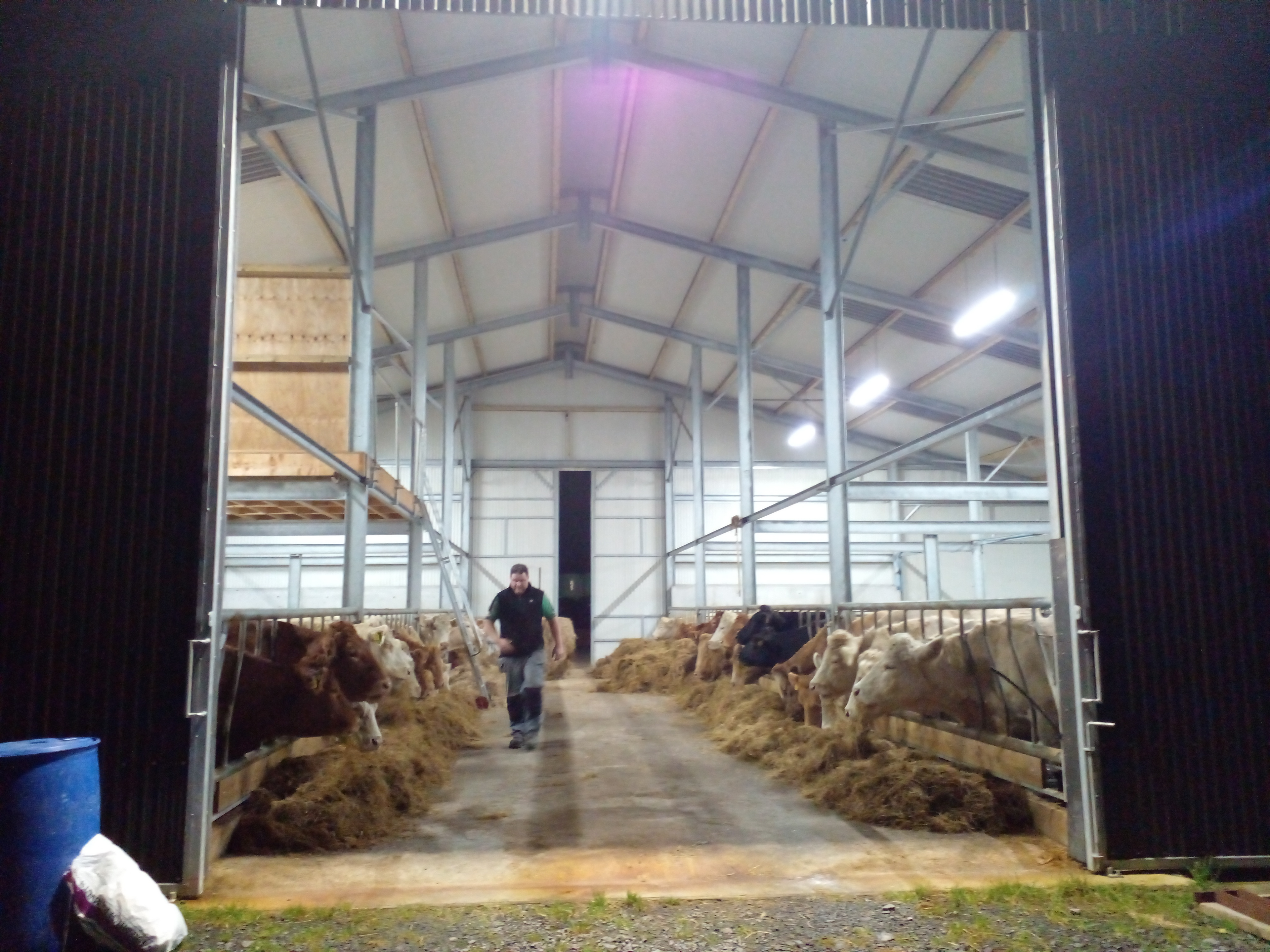
Future Shed, Ireland
Bo Steel Ltd
The first future shed is located in Headford Co Galway on the west Coast of Ireland. When Bó Steel
Ltd was asked to design and deliver the shed for a regular farming customer, the canvas was a blank
one. All aspects of the shed and its internal handling gates needed to be considered and from the
outset Hot Dip Galvanising of all steel components was an obvious choice.
Ltd was asked to design and deliver the shed for a regular farming customer, the canvas was a blank
one. All aspects of the shed and its internal handling gates needed to be considered and from the
outset Hot Dip Galvanising of all steel components was an obvious choice.
In terms of weather, the shed would experience the full onslaught of North Atlantic weather
systems. While the area experiences generally mild weather, the county of Galway is primarily
coastal and experiences far more wet days than some of Ireland's eastern counties. In terms of the
environment within the shed, again galvanic protection of all steelwork was an obvious choice. The
shed would house livestock for 6 to 7 months of the year and consequently the internal climate
within the shed would be of high humidity. In addition, all the lower parts of the shed structure and
internal gates would be in contact with animal dung during animal housing periods. Finally, the
shed represents one of the largest investments in infrastructure in the farms history, for this reason,
the customer required a long service life for his investment. The cost of galvanising was a
discussion point with the customer, however for the reasons outlined, it was a quick decision by all
parties to proceed with hot dip galvanising all components.
Implementation of the decision to galvanise was also an easy process. Bó Steel Ltd already
had a good deal of experience of designing both structures and internal pens for easy processing in
our local galvanising plant. Bó Steel has been utilizing hot dip galvanizing since the companies
foundation in 2007 and through regular engagement with their local Galvanizer, the company had
formalised its own internal guidelines on how best to vent tubular steelwork and also design
complex assemblies with moving components so that the best galvanised finish could be achieved.
The timelines for the project in addition to the logistical planning of site works were all considered
and the local Galvanising company engaged regularly to ensure that sufficient planning occurred to
ensure deadlines agreed with the customer could be met.
The Future Shed has just completed its second winter season in service and all elements of
the Hot Dip galvanise finish on the steelwork are performing. A full inspection was recently carried
out once the livestock had been turned out for the summer months and the customer got a chance to
complete his annual power-washing of the livestock pens and cattle races. Galvanising is the 1st
choice for all similar Bo Steel Ltd projects and will remain so due to longevity, service by their
local galvanising company and peace of mind in relation to product life and quality of finish.
Photographs © Paul Lyons